What is Porosity in Welding: Ideal Practices for Avoiding Permeable Welds
What is Porosity in Welding: Ideal Practices for Avoiding Permeable Welds
Blog Article
The Scientific Research Behind Porosity: A Comprehensive Overview for Welders and Fabricators
Understanding the detailed devices behind porosity in welding is important for welders and producers making every effort for impeccable craftsmanship. From the make-up of the base materials to the intricacies of the welding procedure itself, a plethora of variables conspire to either intensify or reduce the existence of porosity.
Comprehending Porosity in Welding
FIRST SENTENCE:
Evaluation of porosity in welding discloses essential insights into the stability and top quality of the weld joint. Porosity, characterized by the visibility of dental caries or gaps within the weld steel, is an usual problem in welding processes. These gaps, if not effectively attended to, can endanger the structural integrity and mechanical properties of the weld, leading to potential failures in the completed product.
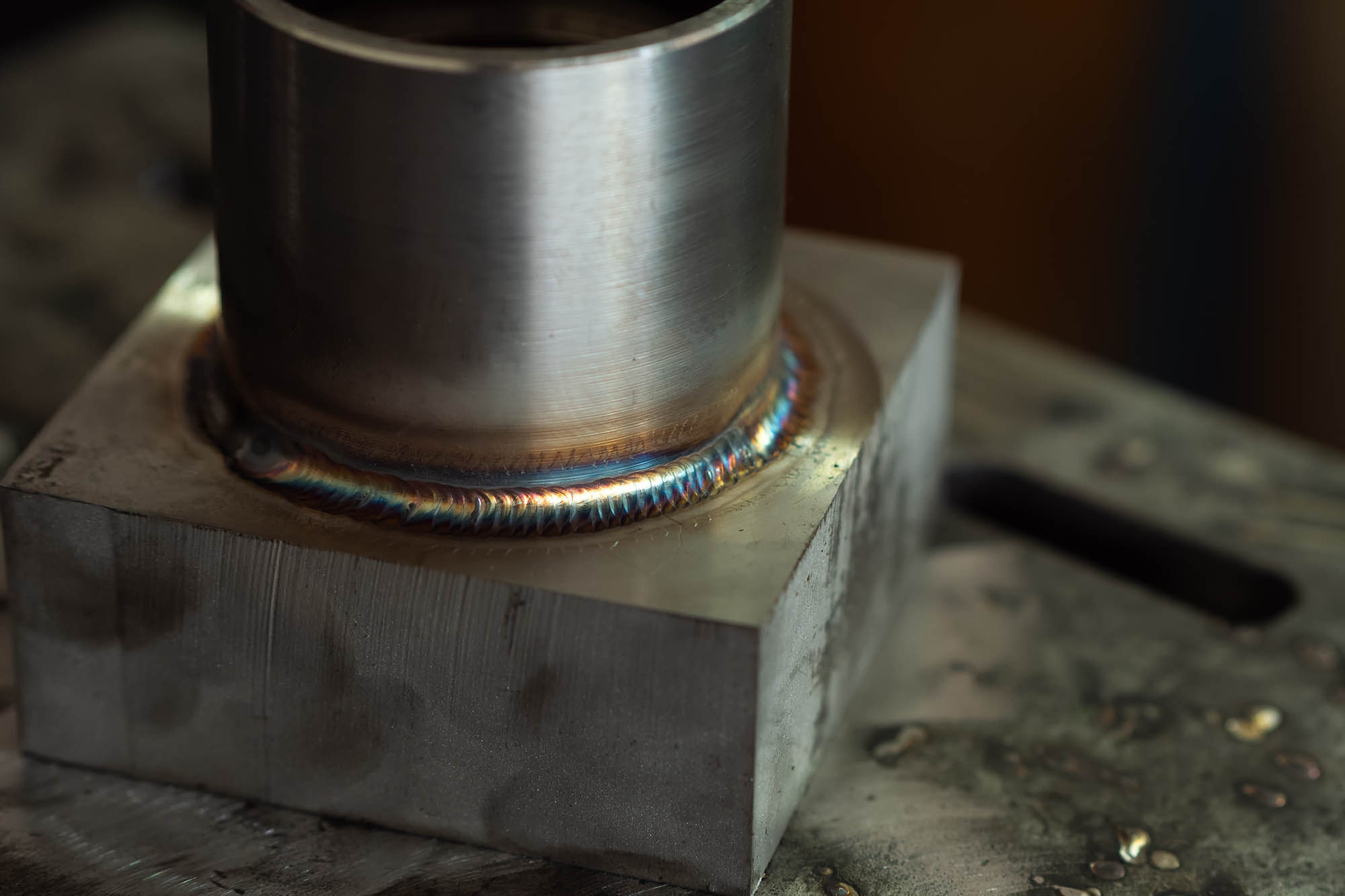
To detect and quantify porosity, non-destructive testing methods such as ultrasonic screening or X-ray inspection are often employed. These techniques enable for the identification of interior problems without jeopardizing the honesty of the weld. By examining the dimension, shape, and distribution of porosity within a weld, welders can make informed choices to enhance their welding processes and achieve sounder weld joints.

Factors Affecting Porosity Formation
The occurrence of porosity in welding is influenced by a myriad of variables, varying from gas securing efficiency to the ins and outs of welding specification setups. Welding specifications, including voltage, present, travel speed, and electrode kind, additionally impact porosity development. The welding strategy utilized, such as gas steel arc welding (GMAW) or shielded metal arc welding (SMAW), can affect porosity development due to variants in warmth distribution and gas insurance coverage - What is Porosity.
Results of Porosity on Weld Top Quality
Porosity formation substantially endangers the structural stability and mechanical buildings of welded joints. When porosity exists in a weld, it develops voids or tooth cavities within the material, minimizing the total stamina of the joint. These spaces work as tension focus points, making the weld extra vulnerable to fracturing and failure under tons. The visibility of porosity likewise damages the weld's resistance to corrosion, as the entraped air or gases within the spaces can respond with the surrounding setting, bring about degradation in time. In addition, porosity can impede the weld's ability to stand up to stress or impact, more endangering the total quality and integrity of see this page the bonded framework. In critical applications such as aerospace, auto, or structural buildings, where security and durability are extremely important, the harmful effects of porosity on weld top quality can have severe consequences, highlighting the value of minimizing porosity via appropriate welding strategies and procedures.
Strategies to Lessen Porosity
Additionally, using the appropriate welding criteria, such as the correct voltage, current, and travel rate, is critical in avoiding porosity. Maintaining a regular arc size and angle throughout welding likewise assists reduce the chance of porosity.

Utilizing the proper welding technique, such as back-stepping or using a weaving motion, can also assist disperse warm equally and lower the chances of porosity development. By applying these methods, welders can effectively lessen porosity and create high-quality bonded joints.

Advanced Solutions for Porosity Control
Executing cutting-edge modern technologies and innovative approaches plays a crucial role in attaining exceptional control over porosity in welding processes. Furthermore, employing sophisticated welding techniques such as pulsed MIG welding or customized ambience welding can additionally aid minimize porosity concerns.
An additional advanced service entails the use of advanced welding equipment. Making use of devices with integrated functions like waveform control and innovative power resources can improve weld top quality and lower porosity dangers. The execution of automated visit the site welding systems with precise control over criteria can considerably decrease porosity defects.
In addition, incorporating advanced monitoring and inspection innovations such as real-time X-ray imaging or automated ultrasonic screening can aid in finding porosity early in the welding procedure, enabling instant rehabilitative activities. Generally, integrating these sophisticated solutions can significantly improve porosity control and enhance the overall top quality of bonded components.
Final Thought
In verdict, comprehending the scientific research behind porosity in welding is vital for welders and makers to produce high-grade welds - What is Porosity. Advanced options for porosity control can better enhance the welding article source procedure and make certain a solid and dependable weld.
Report this page